The project presents a novel approach to the construction of self-supporting thin-shell folded structures. It attempts to take the defining elements of Origami folding and implement them on an architectural scale, creating a full-scale pavilion folded out of of composite aluminum boards which are parametrically designed to fold into shape. Using these principles, a design was made to approximate the growth of a flower which demonstrates an efficient thin shell self-supporting mechanism. A basic folding variable module was created which can be parametrically manipulated in order to form a seamless pattern. The method includes a workflow ranging from initial design to an FEA approach developed especially for the project and optimization algorithms for fabrication.
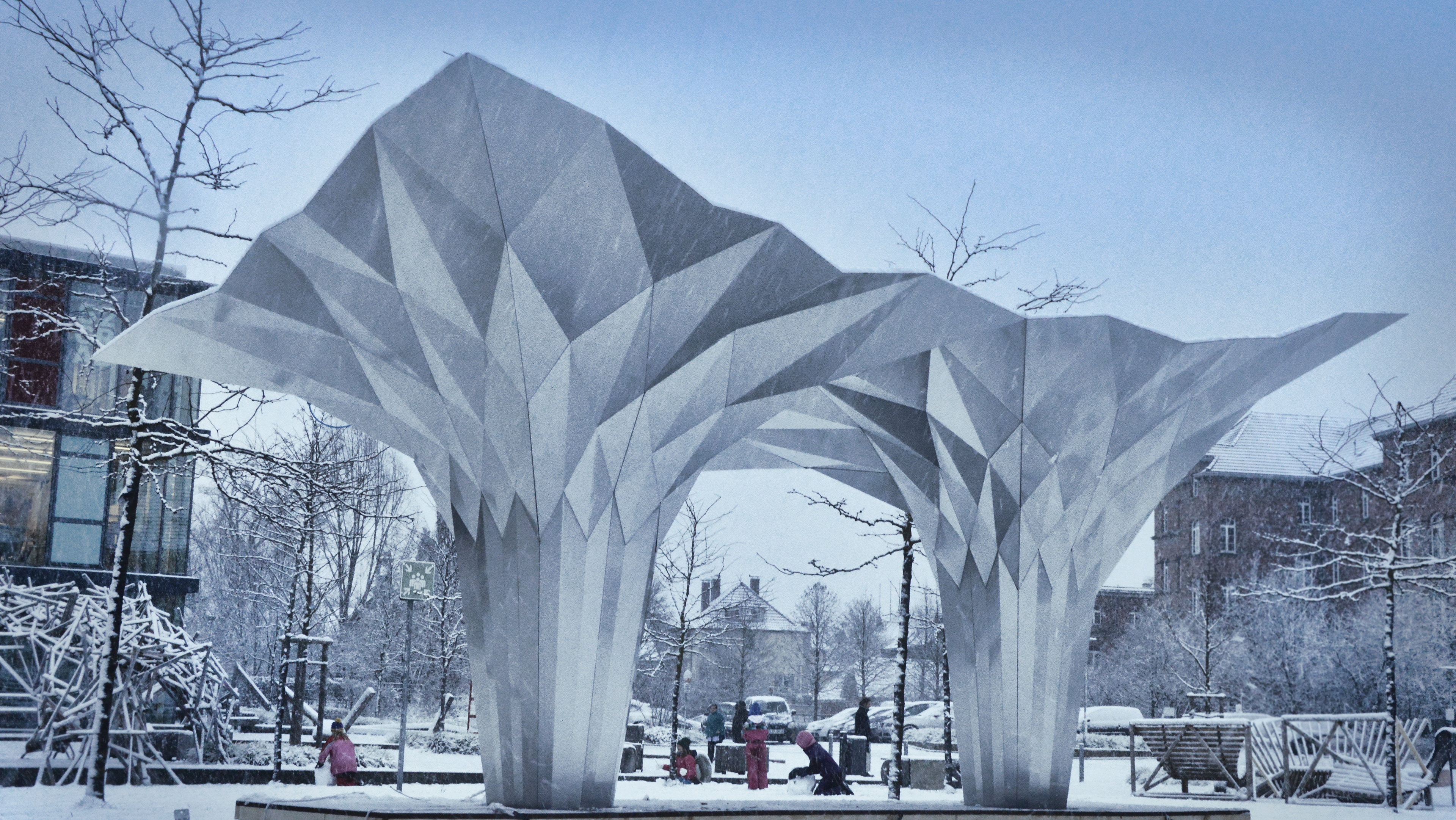
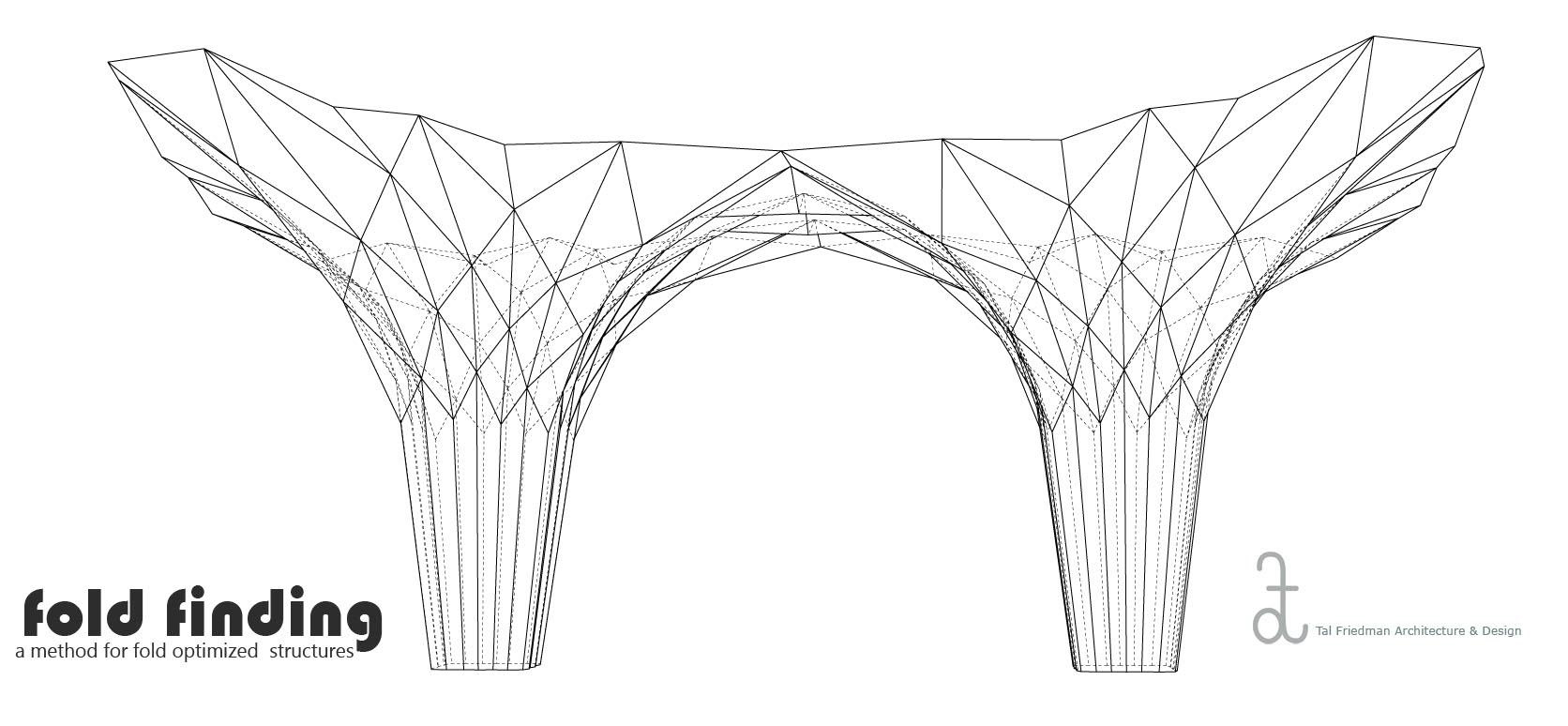

project description:
This project tries to investigate the structural and aesthetic values of Origami inspired folded structures. It is the first fully self-supported cantilever folded structure which uses traditional Japanese paper folding techniques and is folded into stability with no supporting substructure. It, therefore, incorporates a minimalist thin shell from which nothing can be added or subtracted, using its surface rigidity as its structural foundation.The model is based on Origami principles which are modeled with zero thickness and computationally optimized in order to address material thickness and fabrication restraints while producing a seamless looking facade, resembling the original zero-thickness model. In contrast to classical Origami which is designed from a 2d pattern, this project is designed entirely in 3d space and parametrically optimized to unfolded in a process I call "fold finding". This project is a proof concept model to this method, which is defined in my Masters thesis.
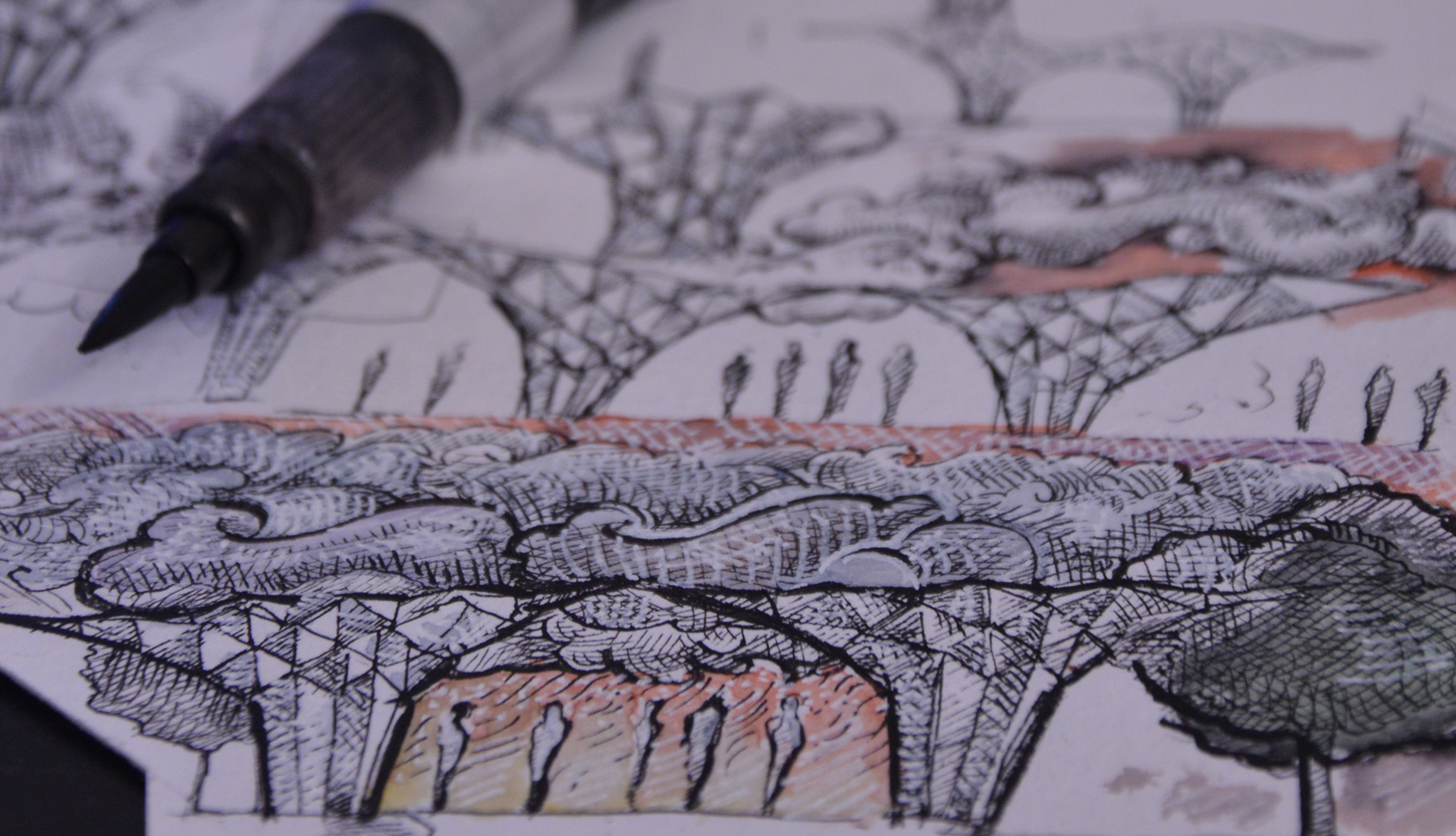


Inspired by the techniques of Origami, the final form is comprised of two "flower" modules were connected together to form a gate structure resembling the outline of a Japanese Torri. In japanese culture, mainly in Shinto, it symbolically marks the transition from the profane to the sacred. I chose to combine the element of a gateway with a pavilion in such a manner that allows for the gate to also be a place of its own, proving sunshade in summer and rain or snow protection in winter.
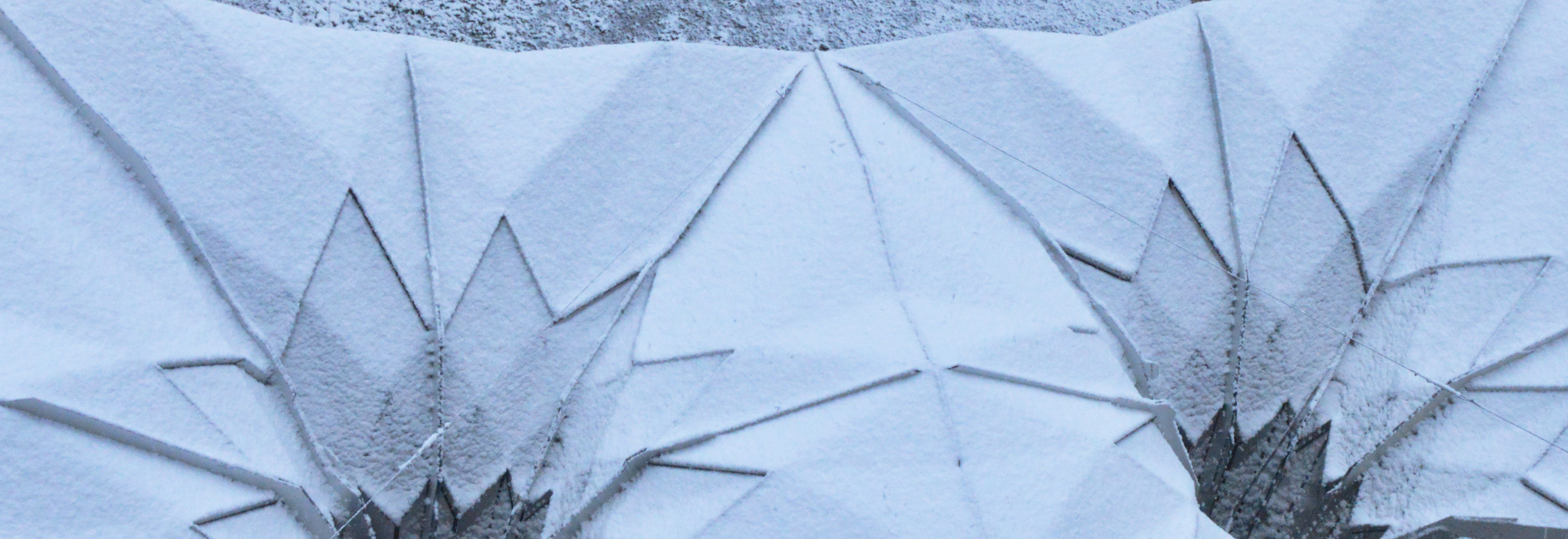
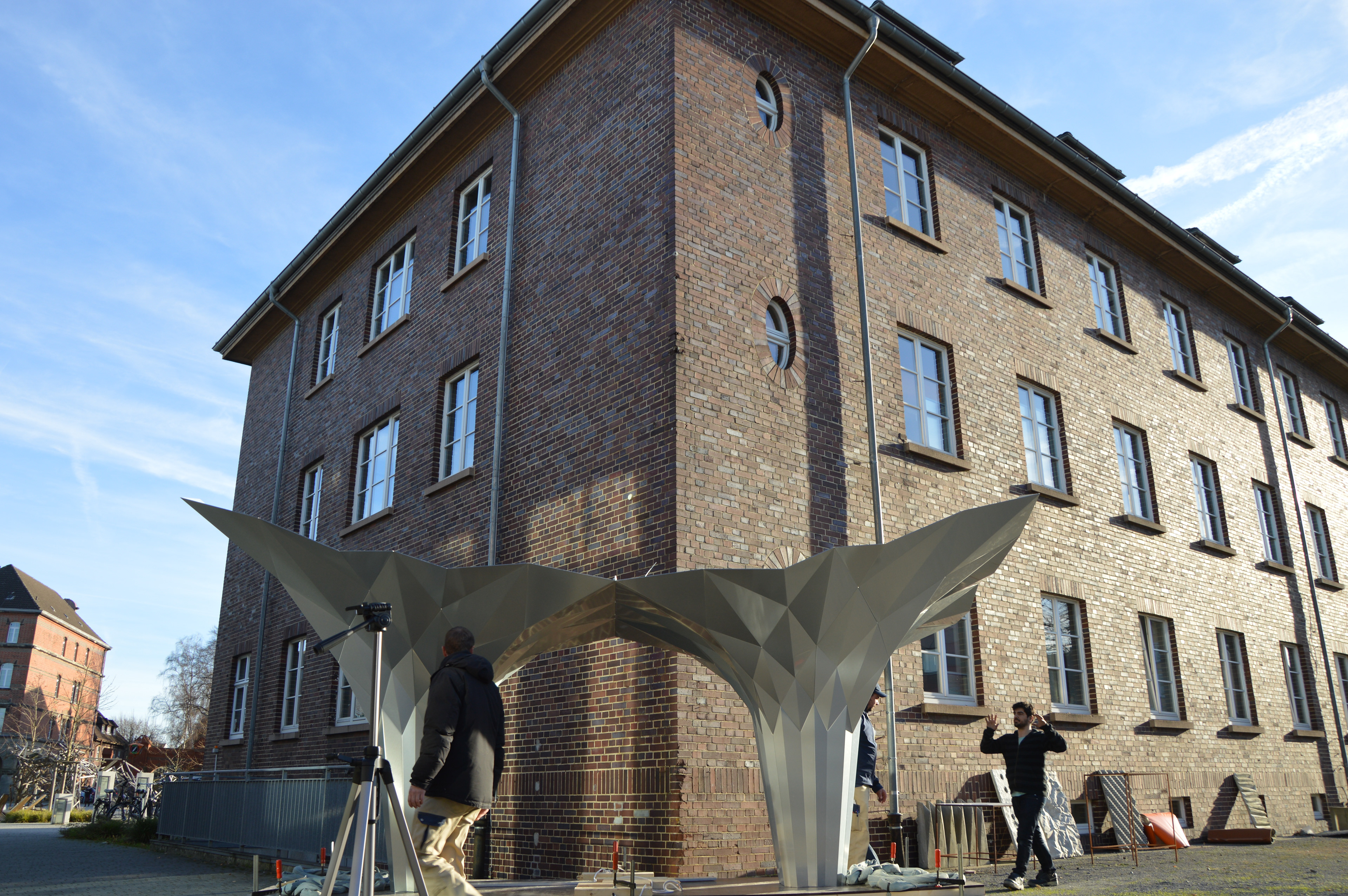


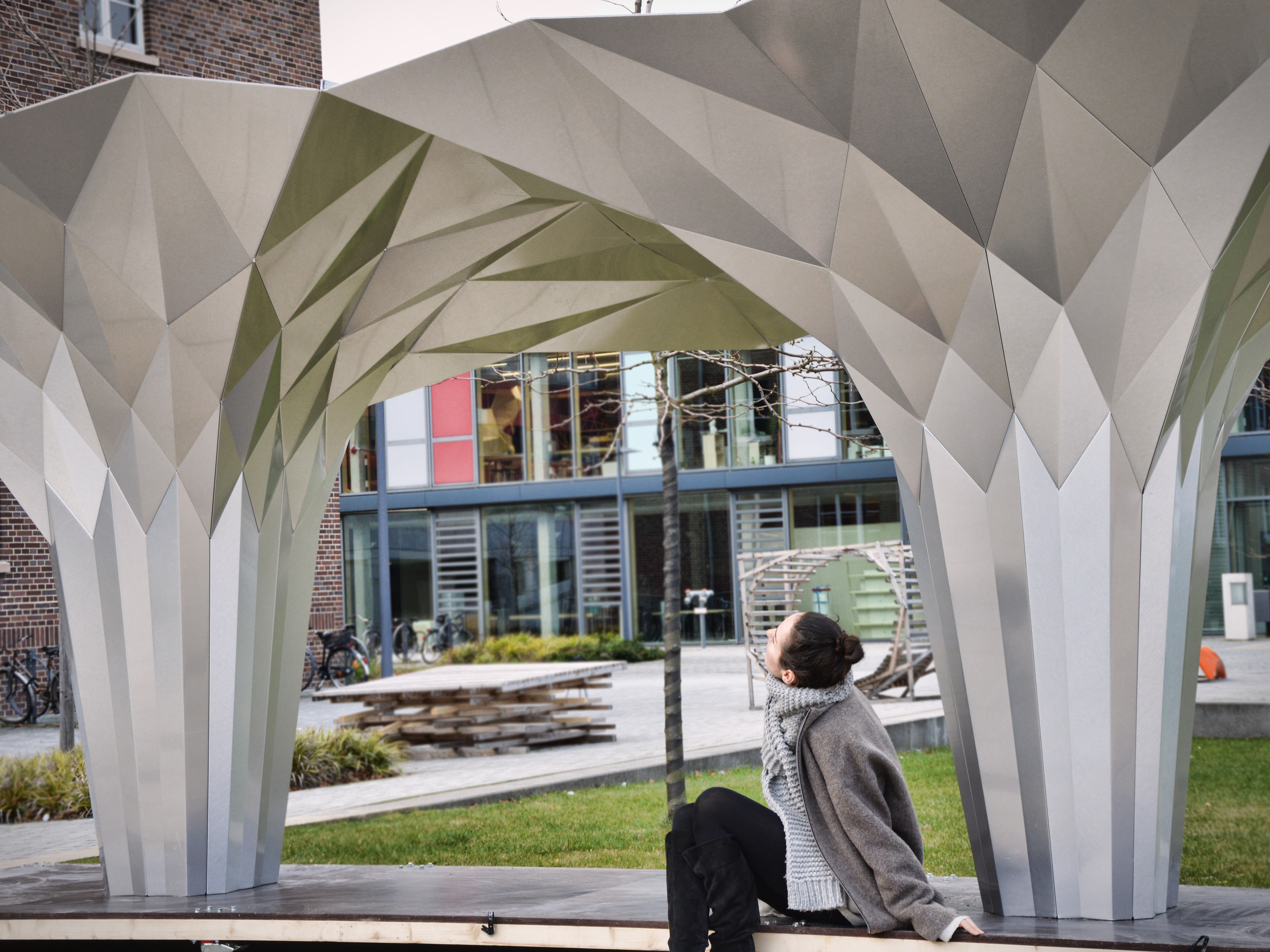
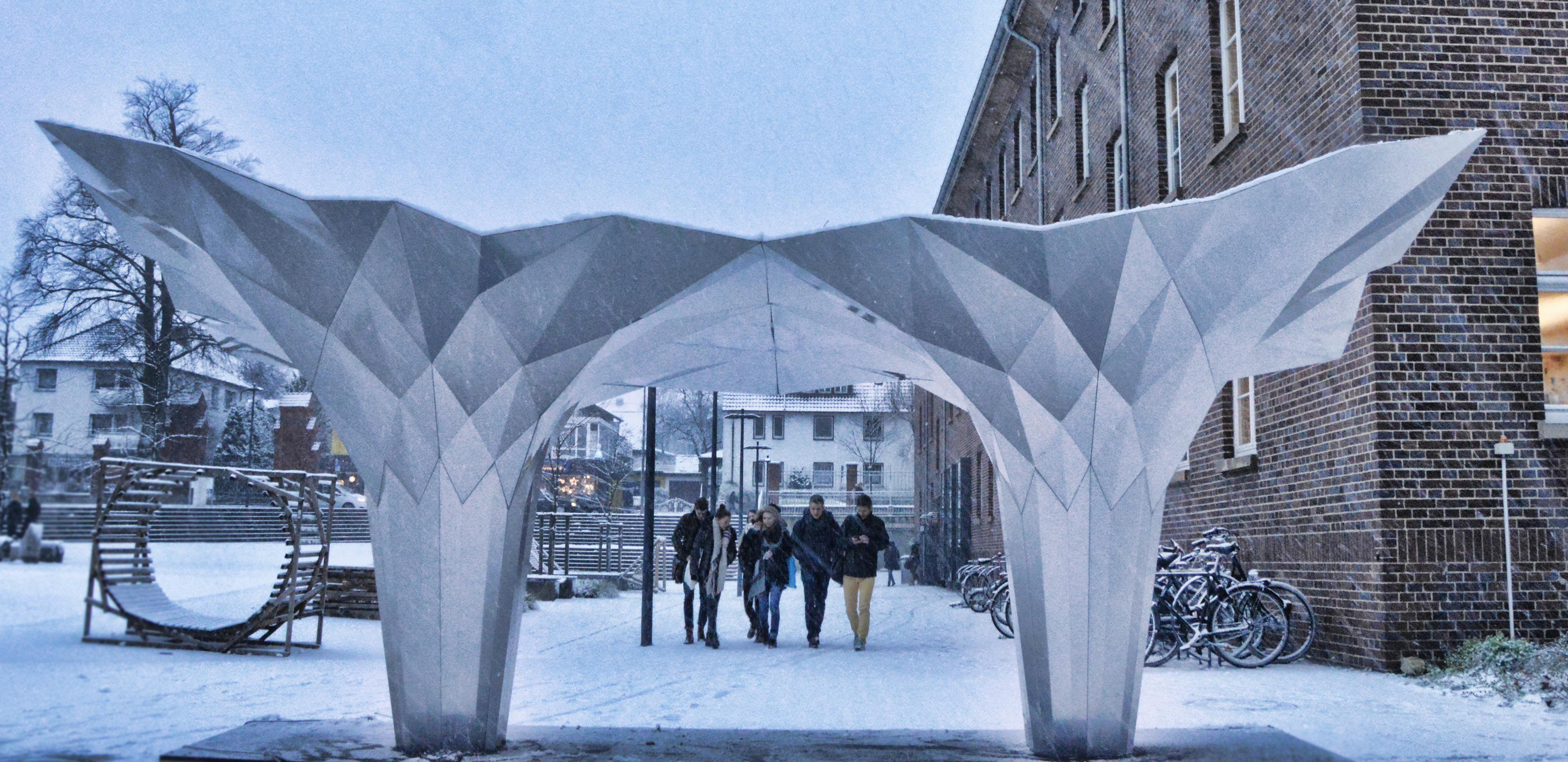
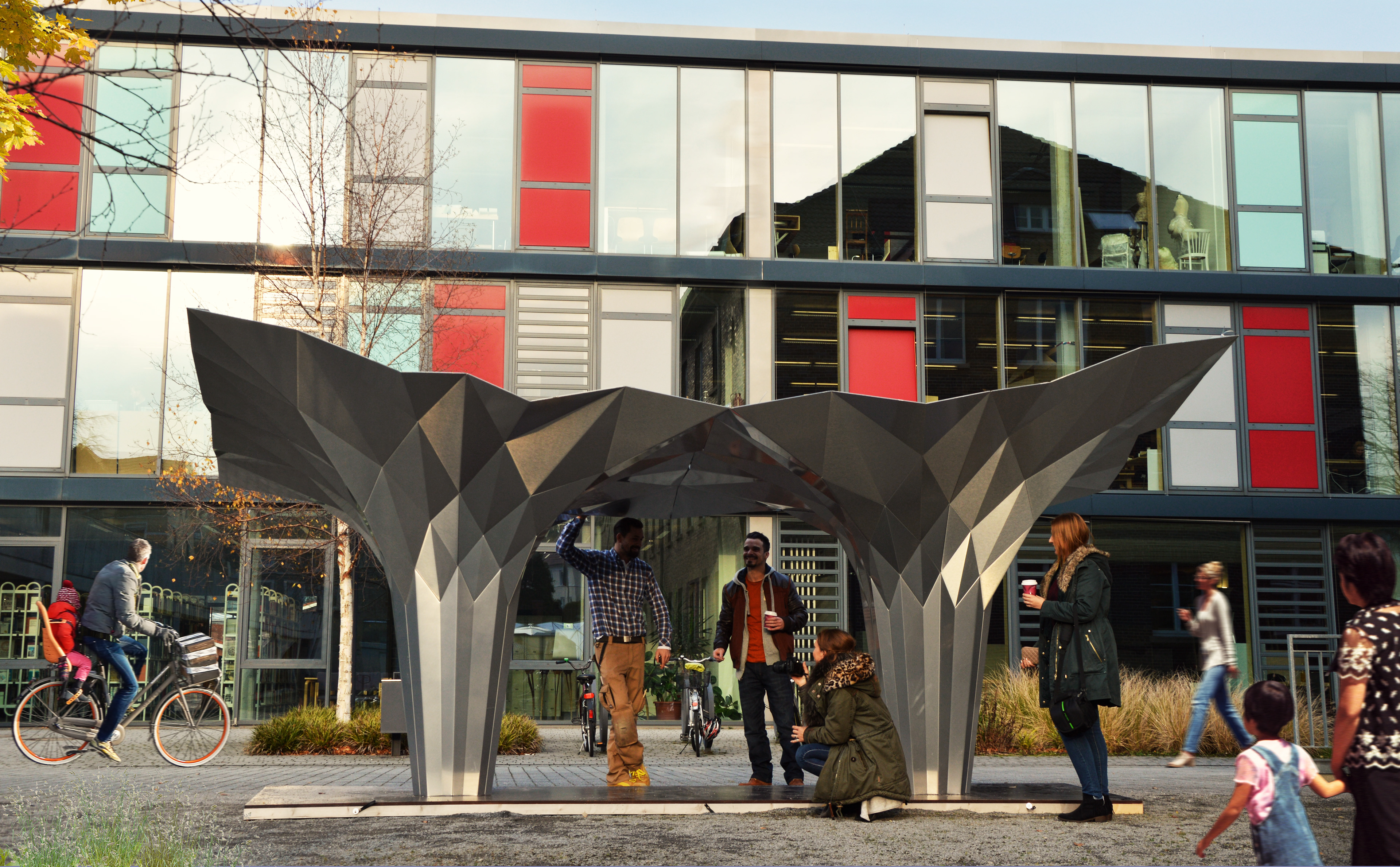
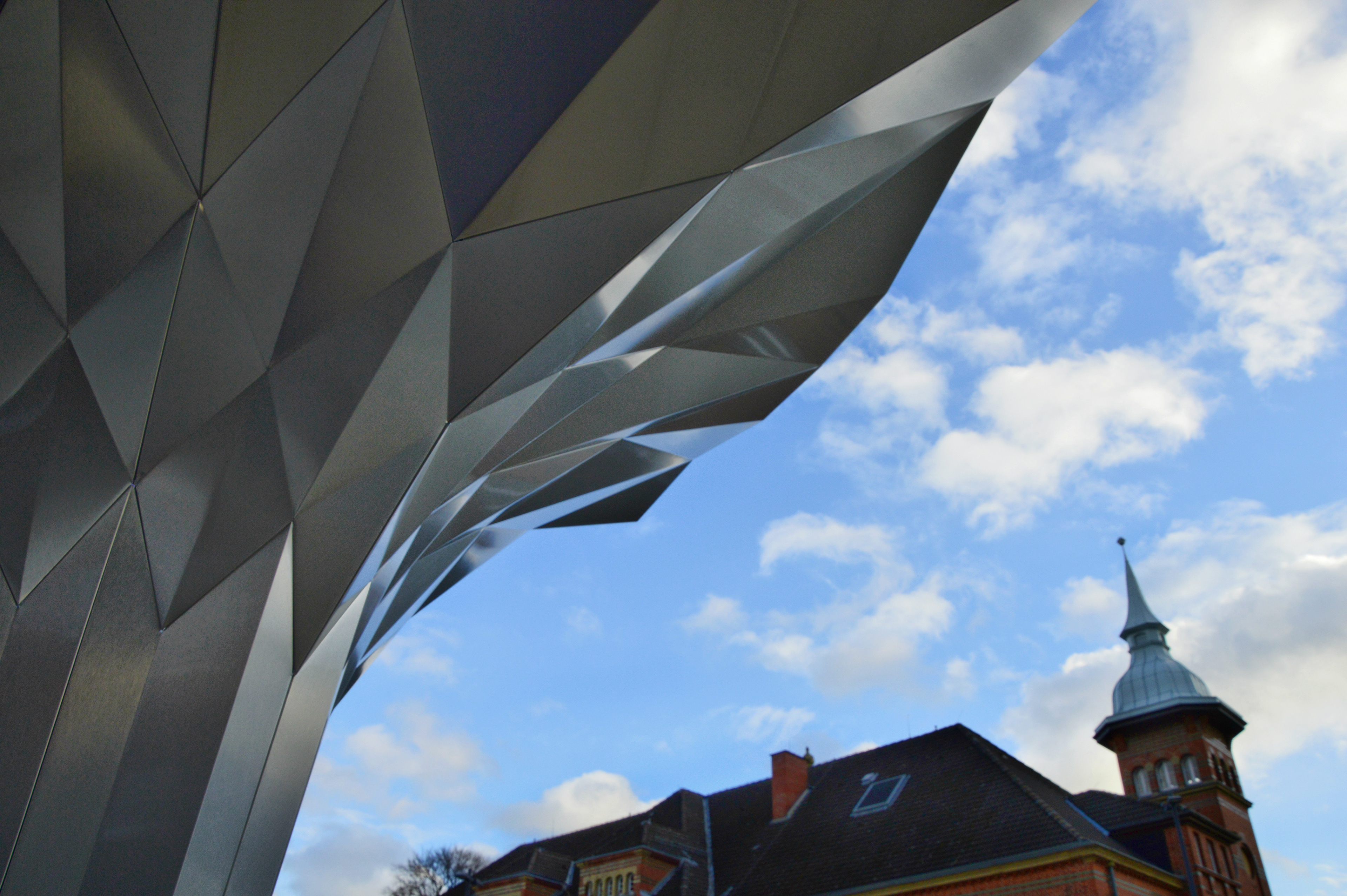


fabrication:
Classical Origami is based on the idea of an idealized zero thickness surface which is approximated by paper. However, in order to upscale this type of design methodology, a material thickness must be taken into account. Starting from an investigation of classical folding techniques, a method for the design and assembly of rigid composite Aluminum boards was developed throughout the project. Algorithms were written in order to calculate and optimize the structure for various fabrication restraints.The project is made to resemble Origami not only in its structural and aesthetically values but also in its fabrication method, which is actually folding the sheets rather than individual panels as is being done today in architecture. Each flower is made for four unique sections which are folded into position. Each folded piece contains around 12-20 interconnected surfaces. This technique saves fabrication time and building tolerance. This project is a proof of concept model concluding that folded structures can be fabricated to full scale while maintaining a self-supported stiffness and stability. Reducing the need for supporting structural systems leads the way to a new kind of true thin shell lightweight structures made from just one material (monocoque).This method may have future application in various fields, including, architecture, deployable structure, shading systems and many more.

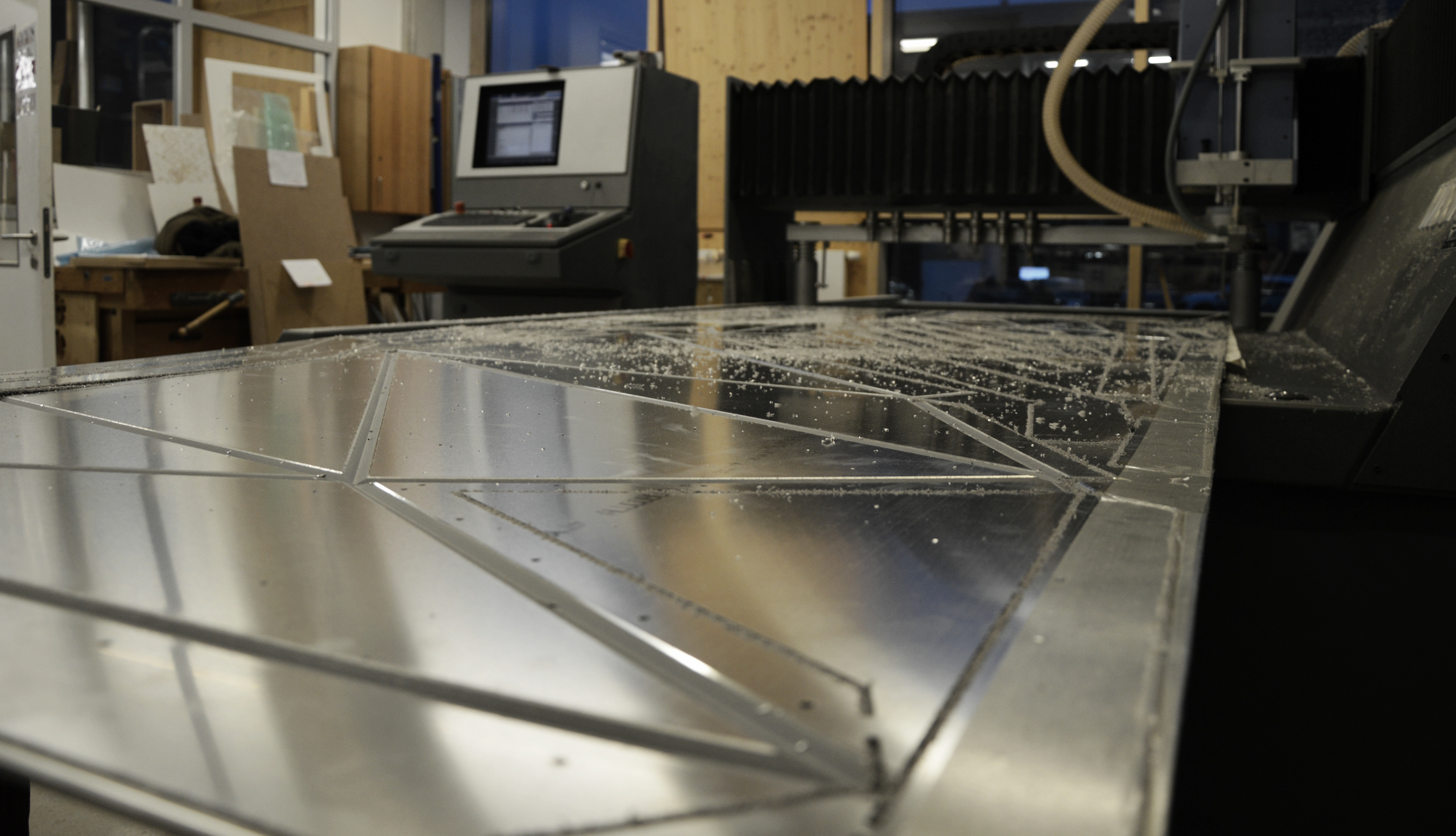
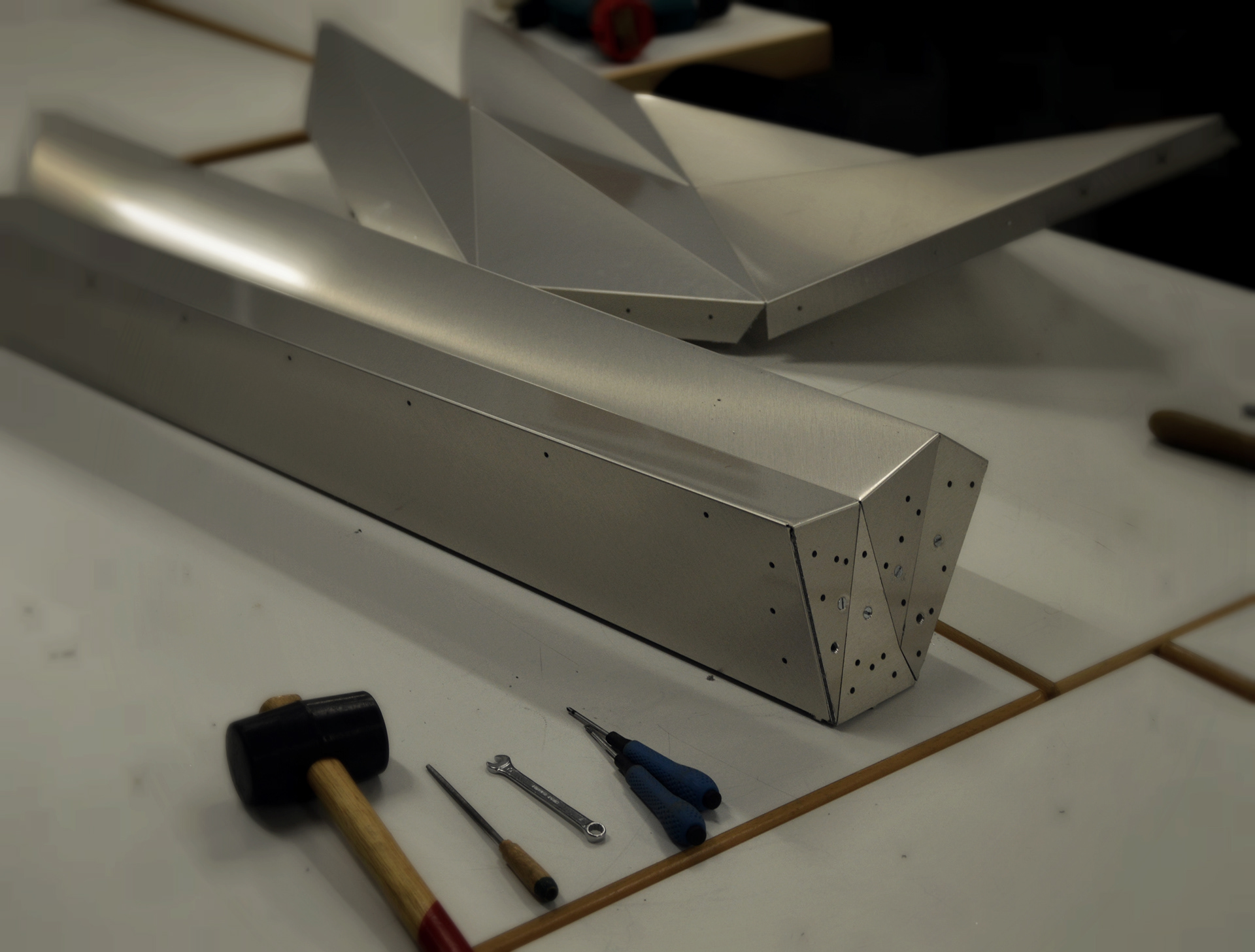
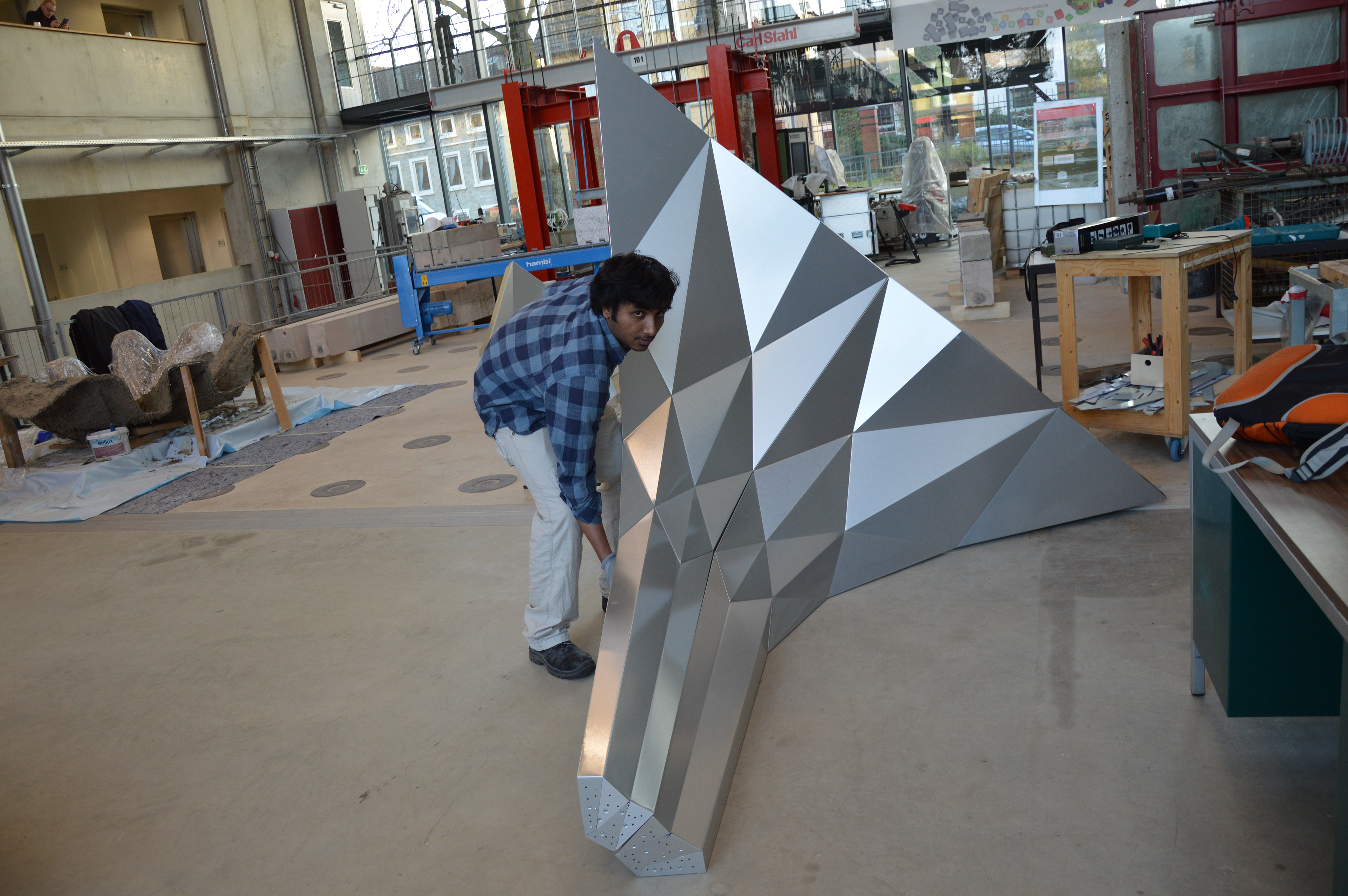
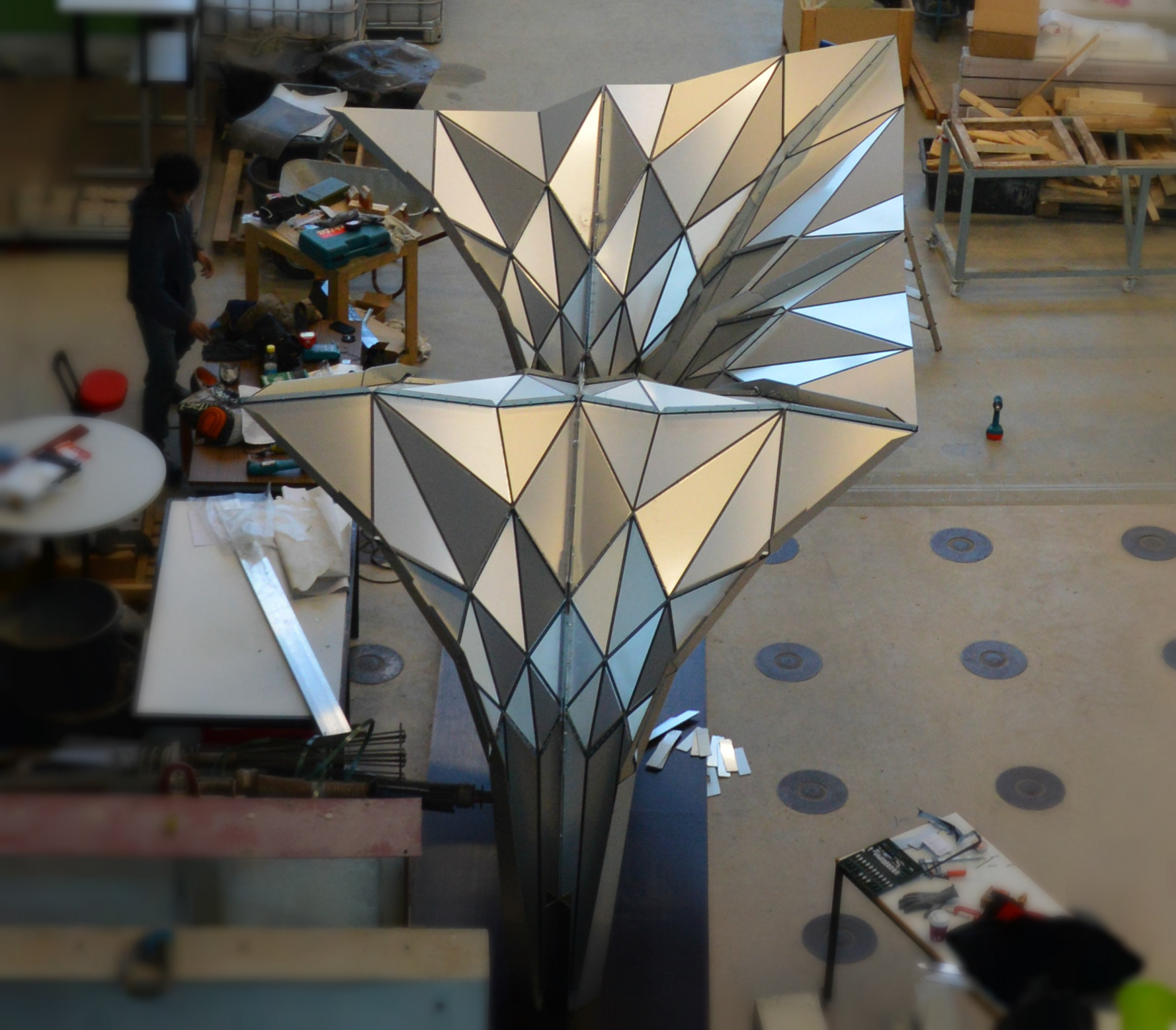

Assembly was pre fabricated in a testing lab and then brought on site.

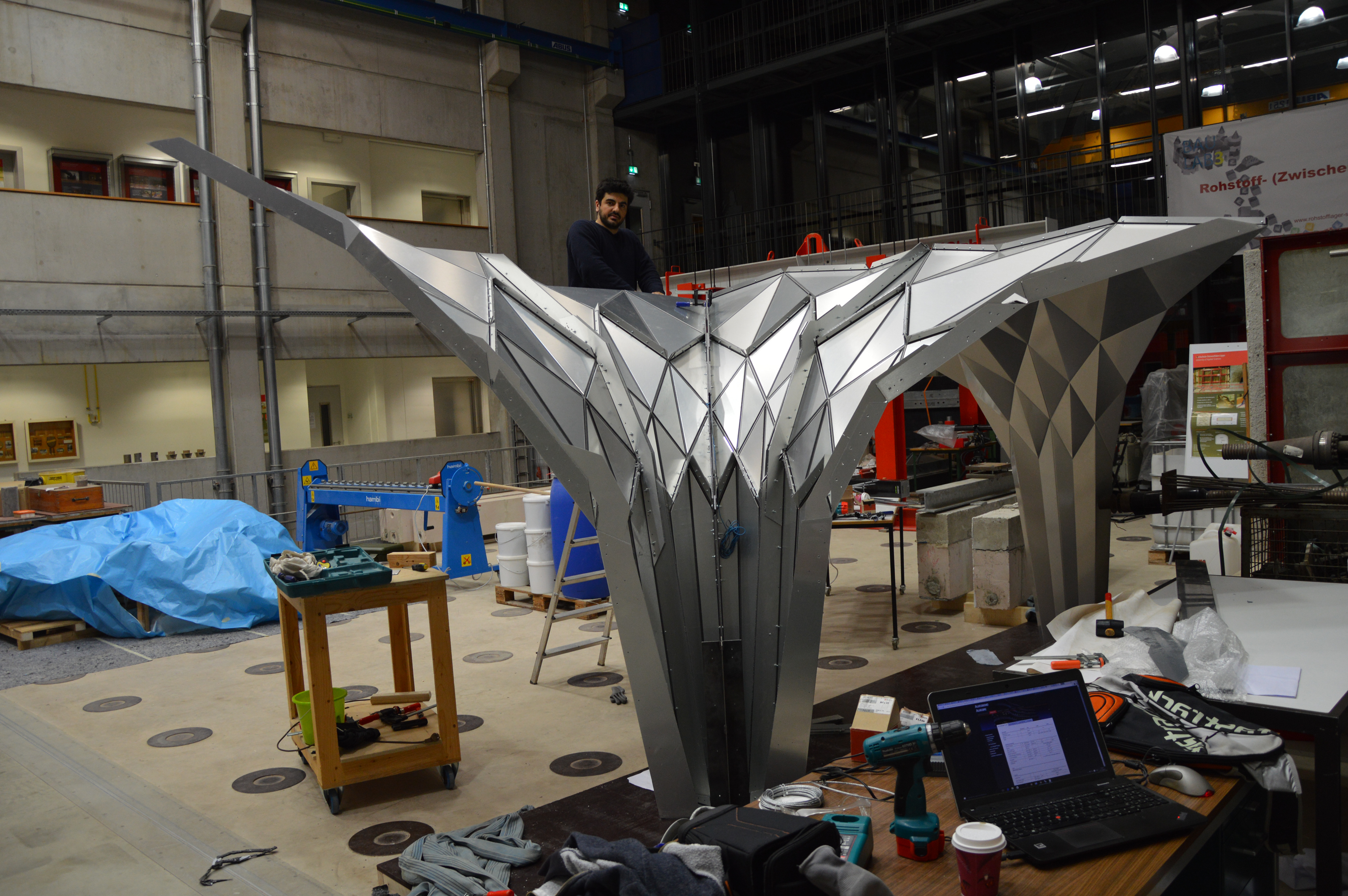
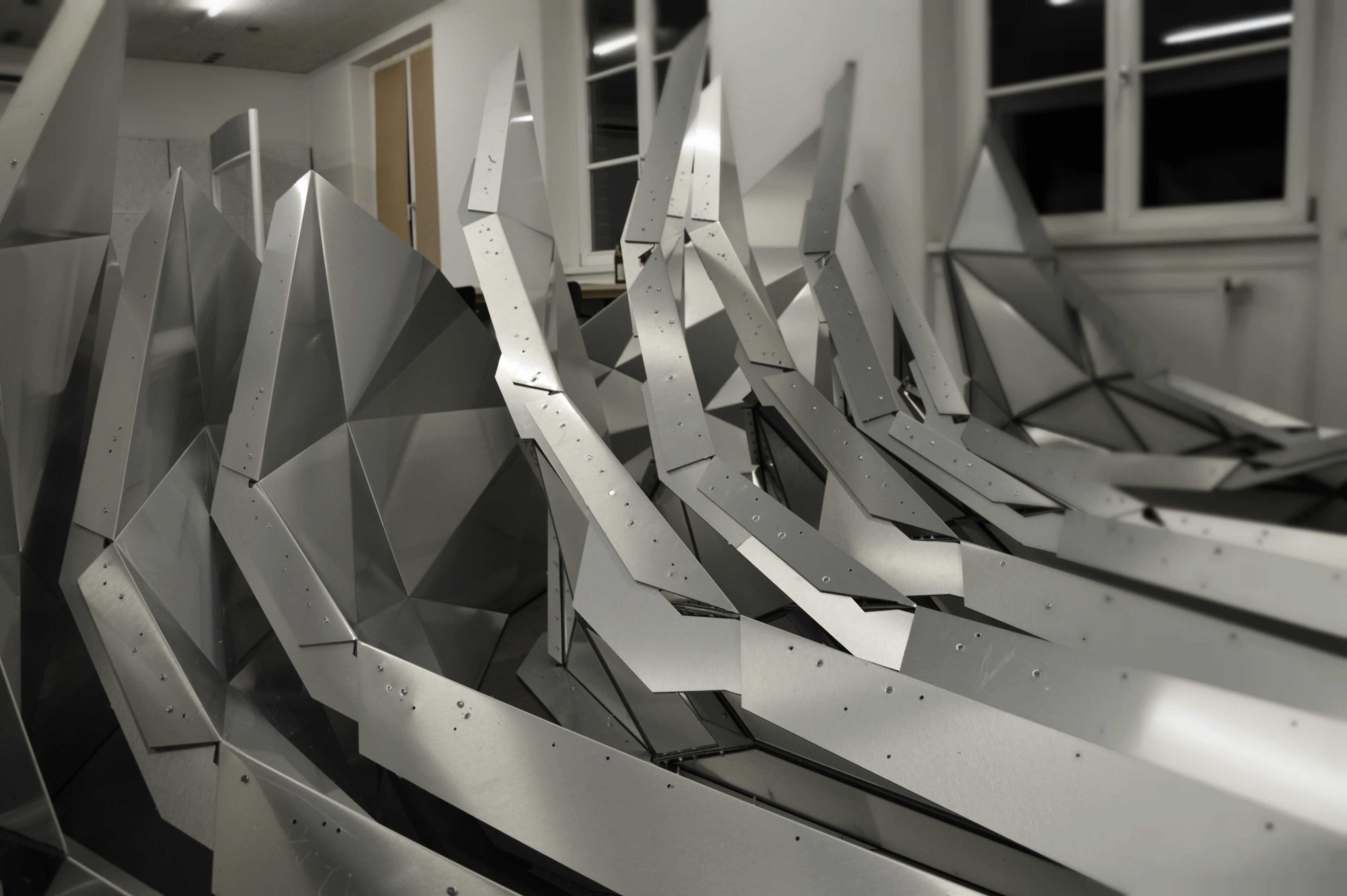
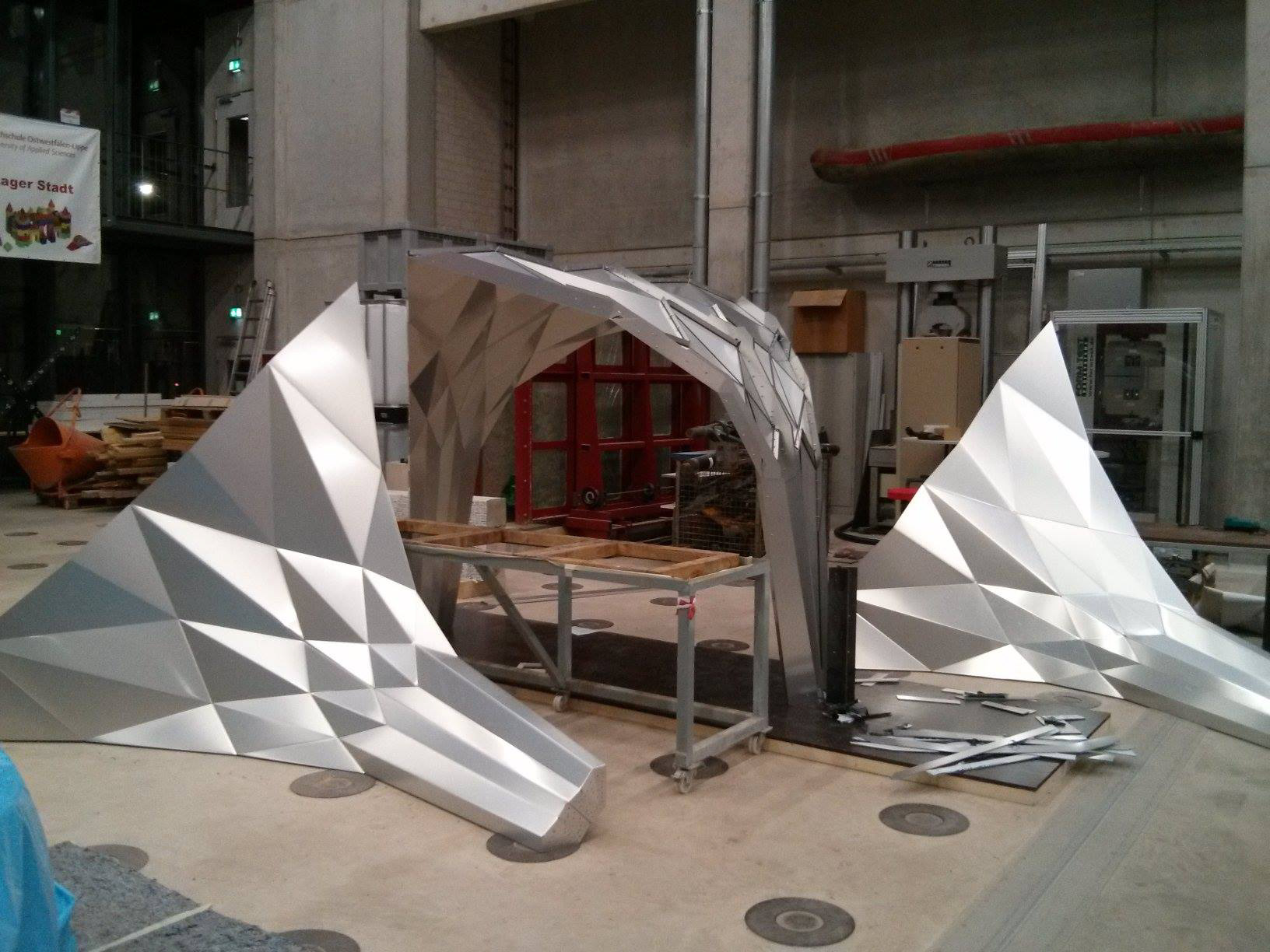


structural:
The structure draws its stability from the rigidity of the surfaces and by locking its fold angles in key locations, it is possible to reach a statically stable structure. A mathematical model was appraised in order to prognosticate the encastre points.
For structural analysis, a computational model was analyzed using the Finite Element method. Due to the complex nature of the composite creased plates, a unique approach was developed on top of the basic formulations of thin shell elements in order to asses the differring thickness rather than treating it as a simple thin shell element. This requires a non linear analysis which can take into account aquimulating material fatigue.

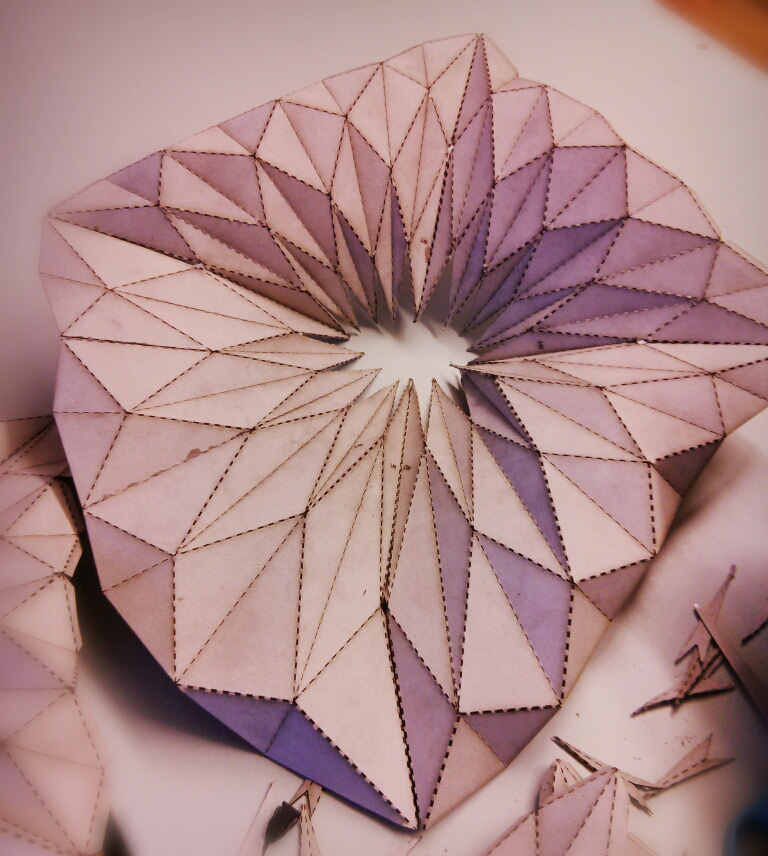
Paper folds models help understand the nature of the folding patern. Later on, material thickness and fabrication will inform the design for scaling to an architectural scale. These moswla were designed through parametric algorithms and laser cut from cardboard.
paper models:
In the process of understanding the nature of folds, various paper models were designed and built, starting oof with thin paper and increasing material thickness gradually untill a parametric paradigm was created that could be used to accomodate the design of 4mm sheets.
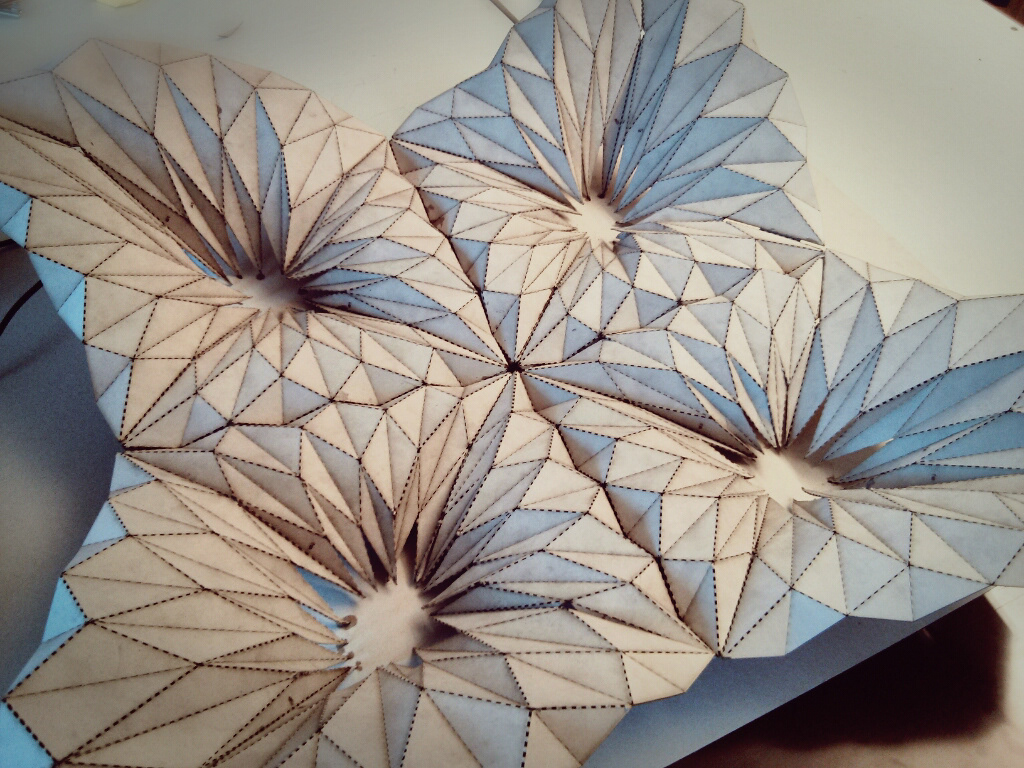
In this project, a "flower" module was developed which was informed by fabrication restraints and optimized for structural behaviour.
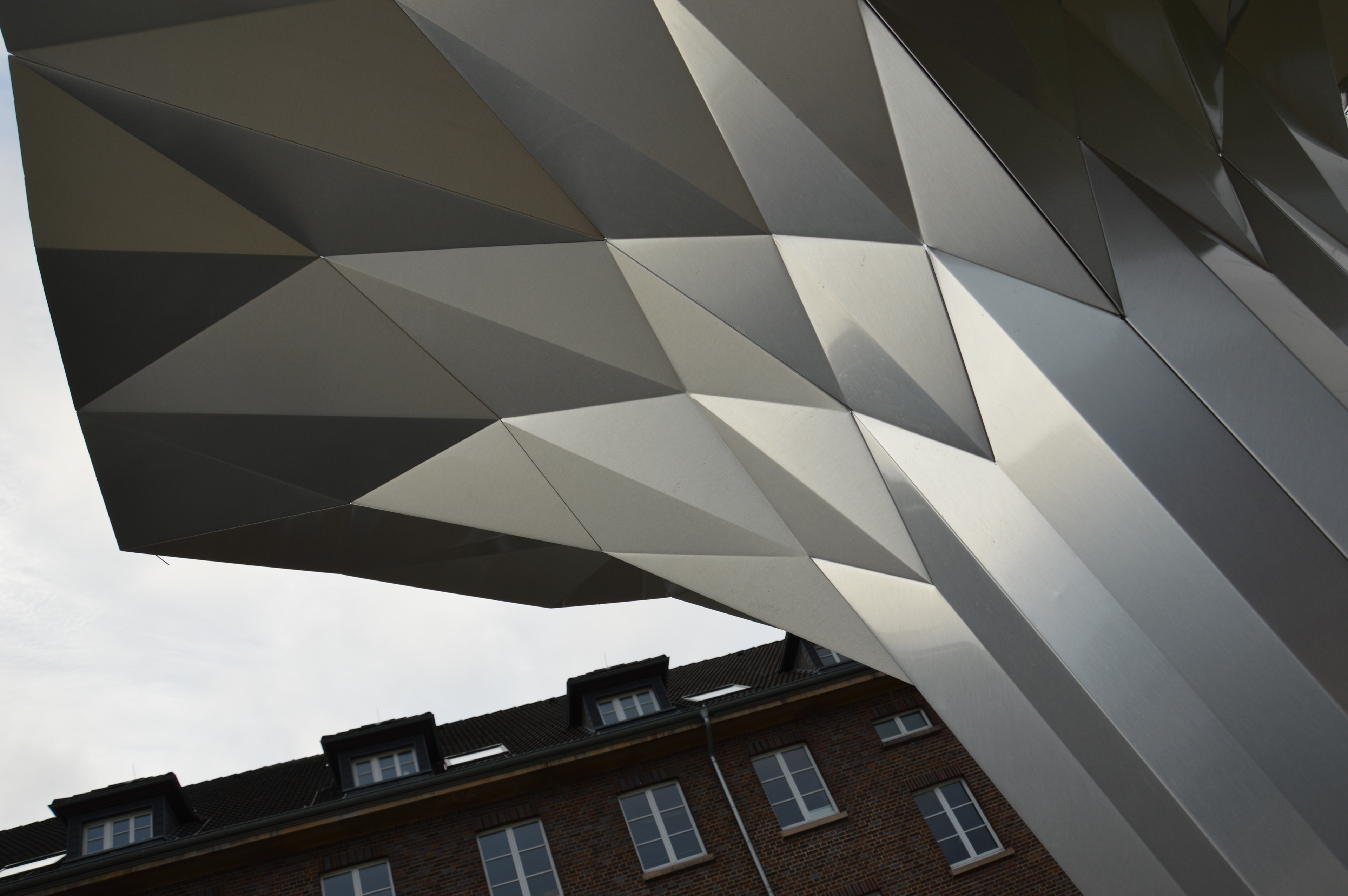

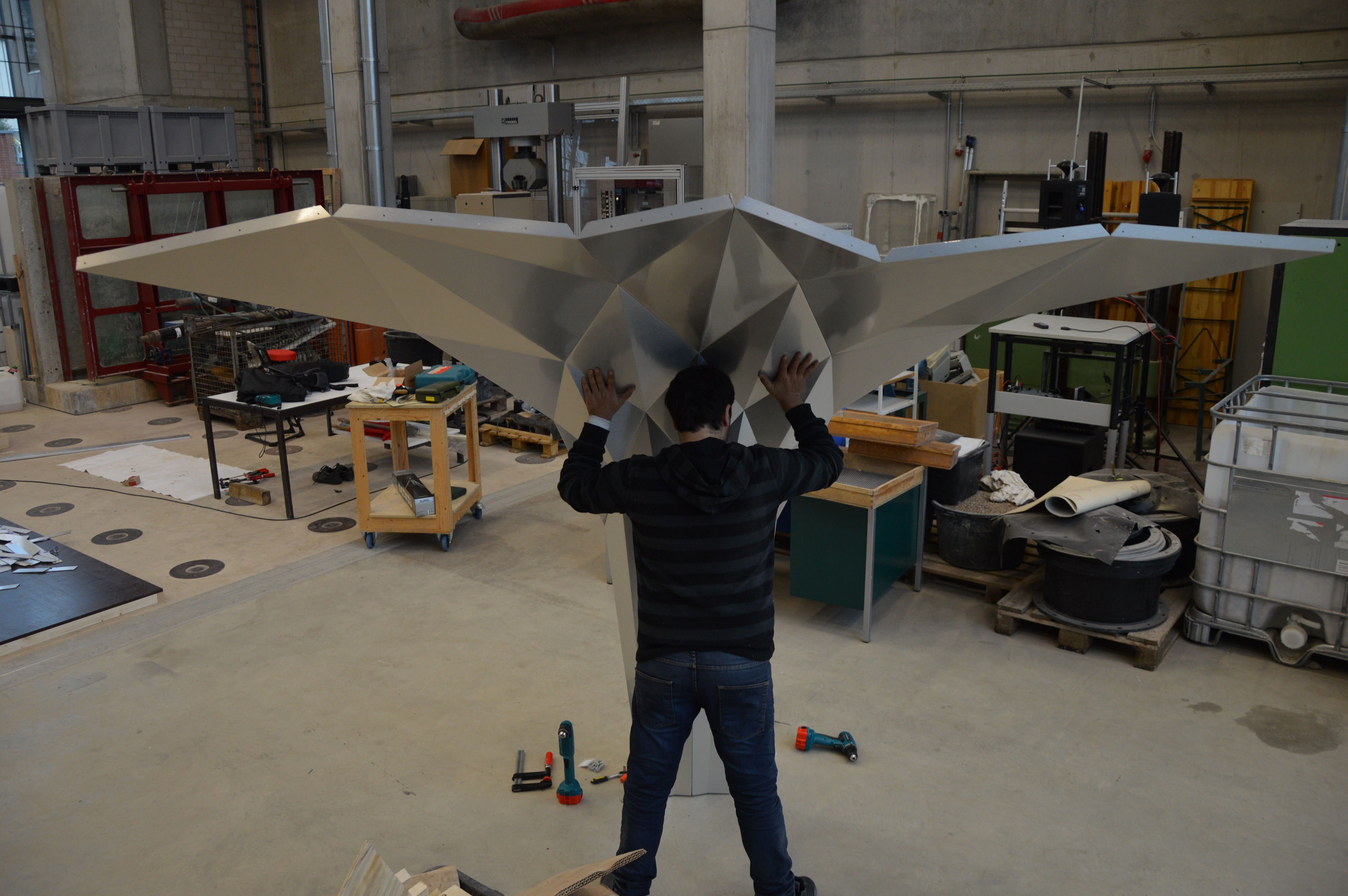

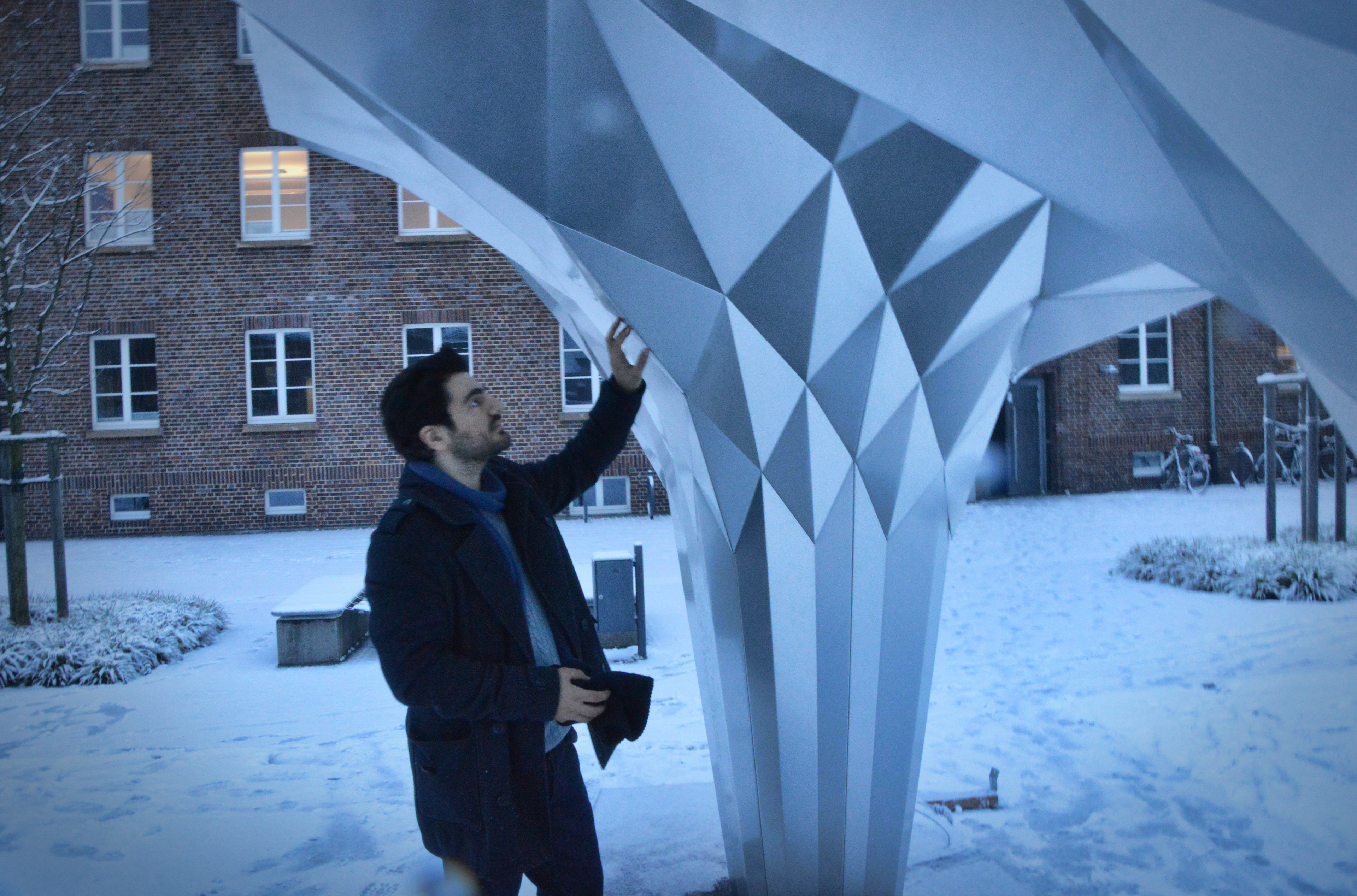
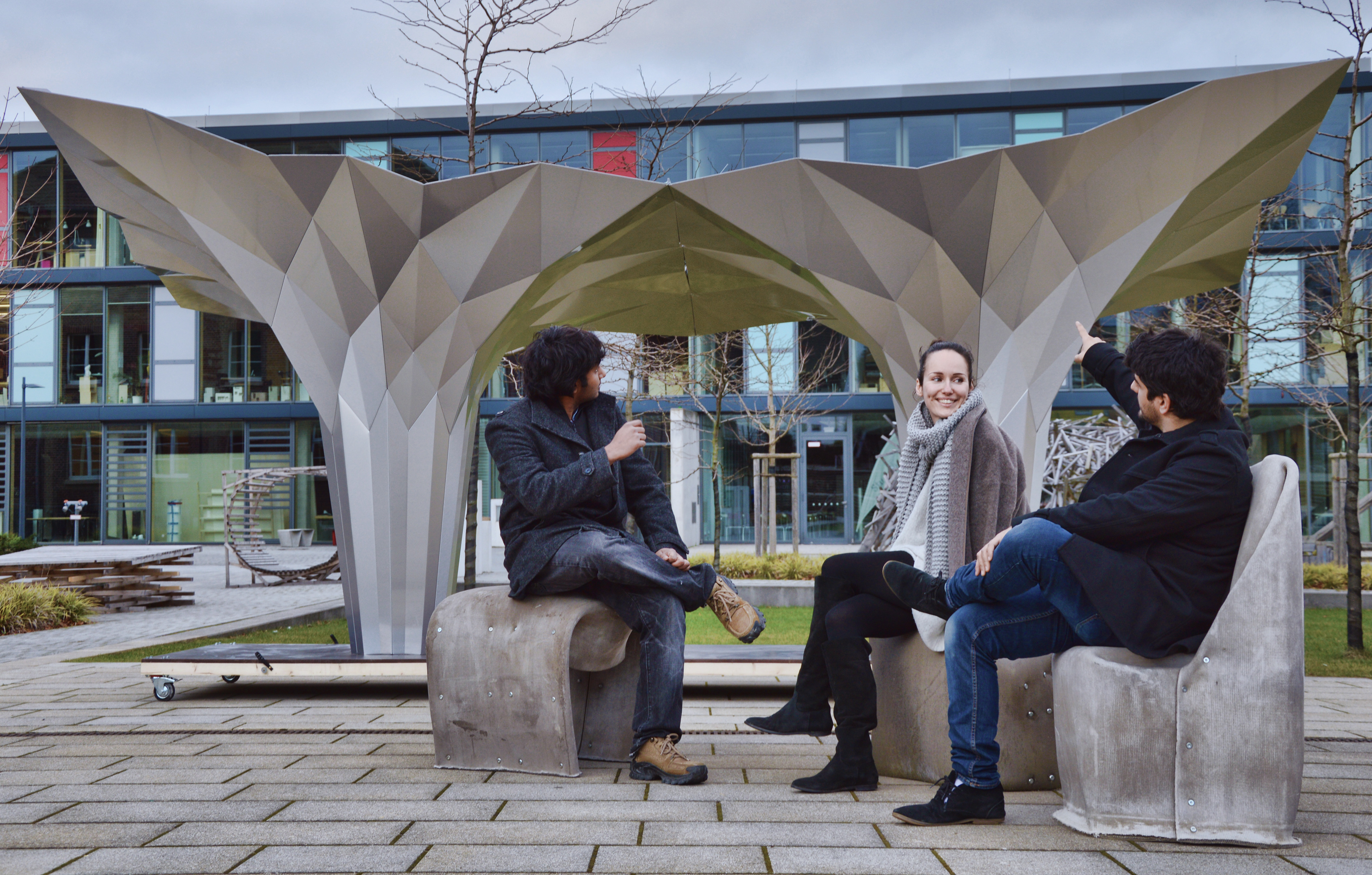

Foldfinding- Origami pavilion
Architect: Tal Friedman
workshop fabrication:
Tal Friedman
Muralimanoj Varadarajan
Guido Brand
Ingmar Rolf
Marcus Opitz
Marcus Dubert
Tal Friedman
Muralimanoj Varadarajan
Guido Brand
Ingmar Rolf
Marcus Opitz
Marcus Dubert
structural analysis:
Tal Friedman
Muralimanoj Varadarajan
Tal Friedman
Muralimanoj Varadarajan
Academic assistance:
Marco Hemmerling
Jens Uwe Schultz
Hans Sachs
Marco Hemmerling
Jens Uwe Schultz
Hans Sachs
photography:
Jenny Stratonowitsch
Tal Friedman
Muralimanoj Varadarajan
Tal Friedman
Muralimanoj Varadarajan
Project done at the Detmold University
of Applied Sciences
of Applied Sciences
supported by 3A composites